目 次
雑科学ホーム
hr-inoueホーム
- 修士論文 別編 -
シランのマイクロ波放電分解による
アモルファスシリコン薄膜作製の試み
シランの分解は、ラジオ波による放電以外にマイクロ波放電や直流放電によっても可能である。今回、マイクロ波を使用した装置を組み、アモルファスシリコン(a-Si)薄膜の作製を試みた。1-4)
装 置
作製した装置のガス系及び電気系を図1'及び図2'に示す。水素希釈シランガスは、窒素でパージできる圧力調整器を通して約1.5atmに減圧した後、精密流量計に入り、ニードルバルブで流量を調節して反応管に導く。ここでマイクロ波をかけて放電させ、適当な温度に加熱した基板上にシリコンを付着させる。反応管は石英製で、その概観を図3'に示してある。
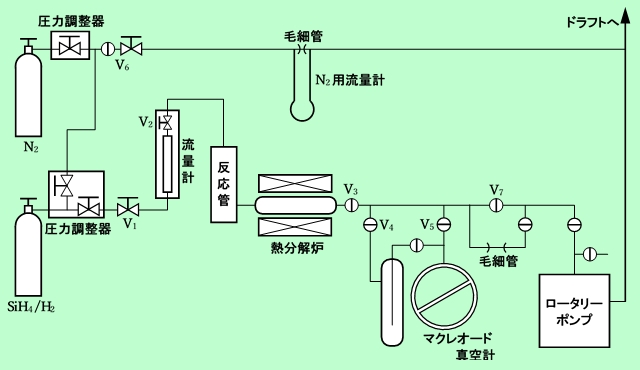
図1' マイクロ波放電によるSi膜作製装置 (ガス系)
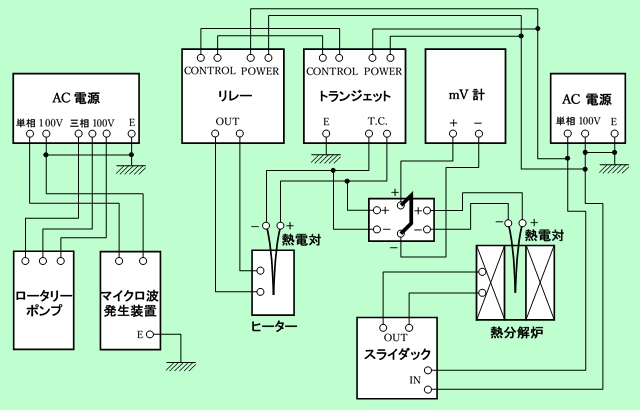
図2' マイクロ波放電によるSi膜作製装置 (電気系)
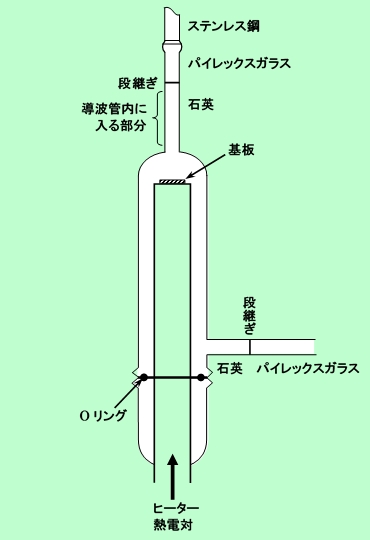
図3' 反応管
放電後のガスは熱分解炉中の石英管に通す。この管内にはステンレス鋼の小片が詰めてあり、700〜800℃に加熱して、未反応のシランを完全に分解する。水素のみとなった排ガスは、パイレックスガラス製の真空系に入り、最終的にはロータリーポンプによってドラフトの中へ、希釈用の窒素と共に放出される。反応管のヒーター及び熱分解炉の温度は、熱電対とリレー回路によって監視、制御される。系全体は、使用前に十分真空排気し(10-3Torr以下)、さらに窒素置換、排気を数回繰り返す。圧力は、回転式マクレオード真空計で測定できる。また、排ガス希釈用窒素の流量は、途中に設けた毛細管の両端の圧力差をオイルマノメーターで読み取る形の自作の流量計で測定する。
種々の部品の一覧表を表I'に示した。
表I' マイクロ波放電によるSi膜作製装置 部品一覧
SiH4用圧力調整器 |
日本酸素 LABO 1301CP |
N2用圧力調整器 |
ヤマト産業 YR-70 |
精密流量計 |
小島製作所 RK 1200 |
主バルブ |
NUPRO ベローズシールバルブ SS-4H-TH3 |
N2用バルブ |
NUPRO プラグバルブ B-4P4T |
真空計 |
木下理化工業 回転マクレオード高真空計 |
配管用部品 |
CRAWFORD スウェージロック
ユニオン
エルボー
ティー |
CAJON ウルトラトール ユニオン
フレキシブルチューブ
トランジションチューブ |
1/4インチ チューブ
SUS316(SiH4用)
Cu(N2用) |
放電条件の検討
今回の目的のためには、安定なプラズマを得ることと、プラズマ中で生成した活性種が基板の位置まで到達すること、という二つの条件を満たすことが必要である。放電を左右する条件としては、マイクロ波の出力、ガス流量、反応容器内圧力、という三つが挙げられる。そこで、それぞれの影響を検討してみた。
マイクロ波の出力は 0〜300W まで変化させることができる。出力を上げるほどプラズマは安定になるが、それだけ反応が激しくなり、活性種はすぐに器壁にSi(おそらく水素を含んでいると思われる)として付着してしまい、基板の位置には届かない。150W 以上では、種々の方法を検討したが、結局基板上にSiを付着させることはできなかった。出力は可能な限り小さくすることが必要である。
ガス流量は多すぎても少なすぎても、プラズマは不安定になる。流量が多い場合には、それに見合ったマイクロ波出力が必要であり、その意味では、あまり大流量にするのは、Siを基板に付着させるためにはよくない。しかし、プラズマの位置が、流量を増すと下方に(基板の方向に)移る傾向があり、この点では流量を増した方が、Siが基板まで届いて付着する可能性が高い。このように相反する要素があるので、ガス流量、という点からのみ条件を考えることはできない。特に、流量を増す、ということは反応容器内圧力を高めることになるわけで、この圧力とのかかわりが大きい。
反応容器内圧力は、流量以外に排気力を変えることによっても調節が可能である。今回は排気系の途中に毛細管を置いて排気抵抗を作ることによって圧力を変化させた。圧力を高くし過ぎても、また低くし過ぎても、プラズマの安定性が悪くなることは、ガス流量の変化の場合と同じである。しかし、排気力を変えて圧力を上げた場合、粉末状Siが生成するという点は特徴的である。流量を一定にして排気力を落とした場合、プラズマ中の活性種が気相で互いに衝突する可能性が高くなり、気相でSiが生成してしまう、ということが、粉末状になる原因であろう。排気力が強い状態で流量を増やした場合は、プラズマ領域を粒子が通過するのが速いので、活性を保った状態で、即ちプラズマ中で、他の活性種と衝突する可能性が低く、大きなSi粒子に成長できないと考えられる。
以上の結果から、目的を達するためには、マイクロ波出力をできるだけ下げ、安定なプラズマが得られる最適の流量、ガス圧力を探す、ということが重要になる。種々の組み合わせを検討した結果、出力 50W、流量 15ml/min、圧力0.3Torrの時が、プラズマも安定で、Siもかなり下方まで付着することがわかった。しかし、この条件でも基板にはごくわずかしかSi膜は付着しておらず、まだ電極等として使用することはできない。
根本的な解決法として、導波管の先端(マイクロ波の出口)の上半分をステンレス鋼の板で覆い、マイクロ波の一部を反射するようにしたところ、基板上にSiを十分に付着させることが可能になった。ただし、マイクロ波の一部は反応管内に入れないのであるから、有効に働くエネルギーは小さくなる。従って、マイクロ波出力は最低100W は必要であった。また、導波管の開口部の大きさ(本来は50mm)も、条件の一つとして新たに加えられることになる。ここで、基板上にSi膜を作ることができる条件をまとめておく。
マイクロ波出力:100〜150 W
ガス流量:9〜10 ml/min
ガス圧力:0.3 Torr
導波管開口部:20〜30 mm
これ以外に、基板をおく水平位置、垂直位置、基板温度等も影響を与えるはずであり、これらの要素も含めて、作製条件と膜の状態との関係をさらに詳しく調べて行くことにした。
膜生成速度
表II'に、導波管開口部、基板の垂直位置(導波管下端からの距離)、及びマイクロ波出力を種々変えた時の膜生成速度の一例を示している。
表II' 各種条件による膜生成速度の変化
(基板温度:250℃、ガス流量:9ml/min、ガス圧力:0.3Torr)
導波管開口部
(mm) |
基板垂直位置
(mm) |
マイクロ波出力
(W) |
膜生成速度
(nm/sec) |
20 |
20 |
100 |
0.258 |
20 |
25 |
150 |
0.249 |
20 |
25 |
150 |
0.222 |
24 |
20 |
100 |
0.214 |
24 |
20 |
120 |
0.259 |
24 |
20 |
120 |
0.211 |
24 |
20 |
120 |
0.223 |
24 |
20 |
120 |
0.237 |
24 |
23 |
120 |
0.194 |
24 |
23 |
120 |
0.189 |
24 |
23 |
120 |
0.198 |
24 |
25 |
120 |
0.145 |
24 |
25 |
120 |
0.130 |
24 |
25 |
120 |
0.135 |
26 |
20 |
100 |
0.051 |
26 |
20 |
120 |
0.054 |
これを見ると、マイクロ波出力の影響はあまり大きくないことがわかる。導波管開口部は小さい方が膜の生成は速い。これは、開口部が大きいと、反応管の上方の器壁に付着する量が増加することによる。ただし、開口部20mmではプラズマの安定性が悪く、また25mm以上にすると、膜の生成が極端に遅くなるので、24mmが適当である。マイクロ波出力も、プラズマの安定性の点から、120Wが最適である。基板の垂直位置に関しては、当然のことながら、導波管に近いほど膜生成は速い。この条件はプラズマの安定性には影響しないので、比較的自由に変えられる。表II'の中から、導波管開口部 24mm、マイクロ波出力 120W のものにつき、膜生成速度の基板垂直位置依存性をプロットしたのが図4'である。プラズマ中で生成した活性種が基板に届く量が、20mmを超えるとかなり減少することがわかる。
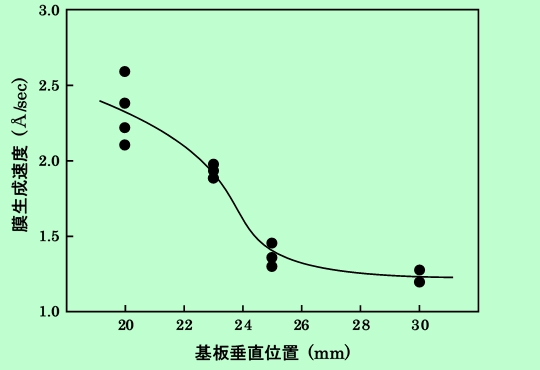
図4' 基板垂直位置と膜生成速度との関係 (基板温度 250℃、ガス流量 9mL/min、
ガス圧 0.3Torr、導波管開口部 24mm、マイクロ波出力 120W)
生成した膜を見ると、かなりはっきりした干渉縞があることがわかる。同じ色の干渉縞の見られる位置では、膜の厚さが、その色のSi中での波長の半分だけ異なっているはずである(表面反射光と、Si/基板 界面反射光とが干渉を起こしており、この二つは膜厚の2倍だけ光路長が異なっている)。従って水平方向に膜厚分布があるわけで、中央が厚く、周辺が薄いと考えられる。そこで、この干渉縞を利用して、基板の水平位置による膜厚の違い、即ち膜生成速度の違いを見積もることができる。その結果をプロットしたのが図5'である。膜厚の異なる試料を数個使用しているので、縦軸には、絶対値ではなく、中央部の生成速度を1とした相対値をとってある。中央から半径5mmの円内では、膜生成速度にそれほど極端な差はない、と見てよいと思われる。
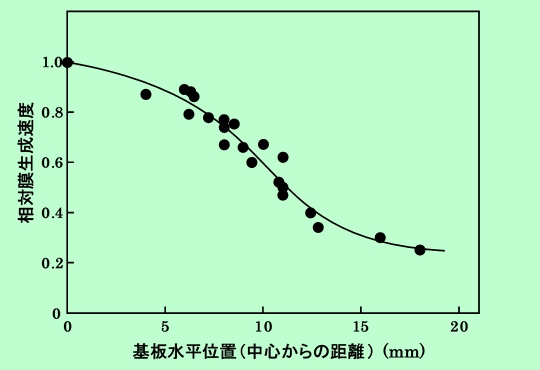
図5' 基板水平位置と膜生成速度との関係 (基板温度 250℃、ガス流量 9mL/min、
ガス圧 0.3Torr、導波管開口部 24mm、マイクロ波出力 100〜150W)
基板温度と膜生成速度との関係を図6'に示す。基板温度は、〜250℃まででは、高いほど膜の生成は速いといえる。今回使用した装置では、これ以上温度を上げることはできない。しかし、図6'の形から、これ以上温度を上げても膜生成速度はあまり変化しないことが予想される。
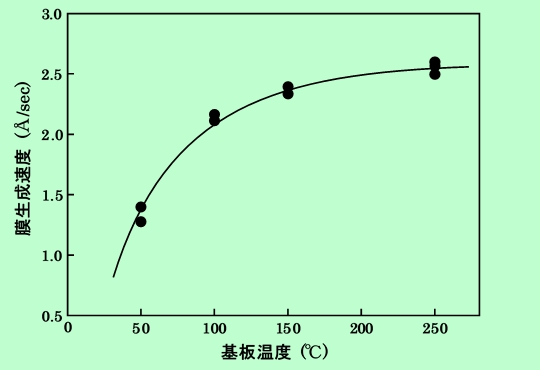
図6' 基板温度と膜生成速度との関係 (ガス流量 9mL/min、ガス圧 0.3Torr、
基板垂直位置 20mm、導波管開口部 24mm、マイクロ波出力 120W)
X線回折スペクトル
作製したSi膜のX線回折スペクトルを測定したところ、結晶Siの(111)面、及び(220)面からの反射が観測された。これは大阪大学で作製したμc-Siと全く同じであり、この装置ではアモルファスにならず、微結晶を生成しているということがわかった。アモルファスにするには、さらにSiH4の分圧を上げ、マイクロ波出力を下げる必要があるが、前に述べたように、マイクロ波出力はこれ以上小さくすることはできないので、事実上、a-Siの作製は不可能であろう。マイクロ波放電によってa-Siを作製するには、より大容量のシステムが必要である。
光学的性質
作製したμc-SiのUV-VISのスペクトルを図7'に示す。吸収端は約700nmで、この値は膜の作製条件によらず、ほぼ一定であった。従って、光学的バンドギャップは1.7〜1.8eV ということがわかる。これは一般のa-Si、μc-Siの値と同じである。また、500nmにおける吸光係数も104〜105cm-1であり、一般に言われている値と一致している。
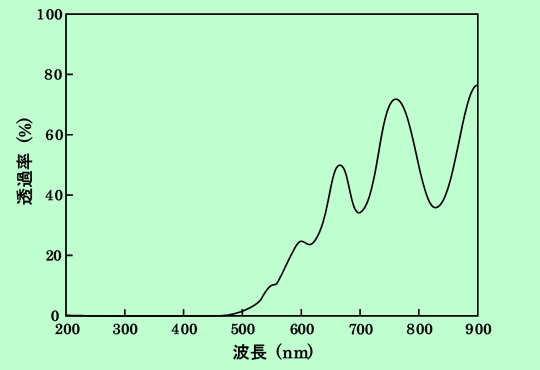
図7' マイクロ波放電によって作製したSi膜のUV-VISスペクトル
長波長領域に現れる干渉パターンは膜厚決定に用いられるが、このパターンの鋭さ(極大、極小の差の激しさ)が試料によって異なり、作製条件との相関性もはっきりしない。しかし全般に、大阪大学で作製した膜と比べてパターンが鈍くなっている。これは、膜厚が一様でないこと(前述)、及び表面の干渉性が悪いことが原因であると思われる。実際に肉眼で試料を観察してみても、澄んだ赤褐色ではなく、やや濁った茶褐色に見えることが多く、表面の乱反射がかなりあるようである。
電極特性
a-Siの場合と同様にして、鏡面仕上げステンレス鋼基板上に作製したμc-Siについて、その電極特性を測定した。図8'に電流-電位曲線を示す。
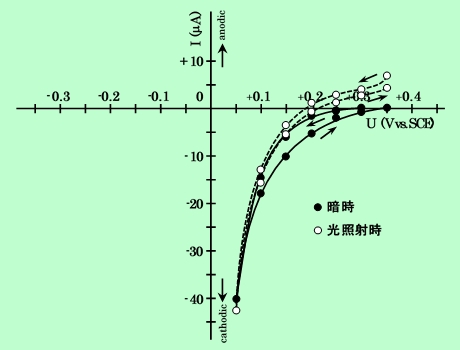
図8' マイクロ波放電により作製したSi膜の電流-電位曲線(Fe(III)/Fe(II)水溶液中)
図のように、非常に早くからカソード電流が立ち上がり、電流値も非常に大きい。これは、バンドの曲がりが小さいというよりも、ステンレス鋼基板が直接に、或いはごく薄いSi膜を通して溶液に接触している、と考えた方が妥当であると思われる。即ち、μc-Siは基板上に島状に付着している、と考えられる。それでも、図8'に示した電極では、かなりの光電流が観測されており、また、開放電圧も0.16V という値が得られている。しかし、試料によっては、カソード電流の立ち上がりがさらに急激で、光効果もほとんど見られないものもあり、また電極特性の作製条件に対する依存性もはっきりしない。ただし、膜生成速度の速いものほど電極特性が悪い、という傾向はあるようである。
いずれにしても、小規模のマイクロ波放電装置ではプラズマの制御が困難で、再現性のある良質の薄膜の作製には至らなかった。
付記 マイクロ波放電によるSi膜作製装置 操作法
操作手順(図1'、2'参照)
1. ロータリーポンプ ON. V3まで排気
2. liq. N2 トラップ セット
3. ドラフト ON
4. 真空度確認(10-3Torr以下)
5. N2 元栓 OPEN
6. N2 減圧弁 OPEN(10atm)
7. 基板 セット
8. ヒーター 及び 熱電対 セット
9. V3 OPEN
10. 真空度確認(10-3Torr以下)
11. ヒーター ON. 1時間加熱
12. V2 OPEN(フロートが落ちるまで放置)
13. V2 CLOSE
14. パージバルブ OPEN
15. V1 OPEN
16. SiH4 減圧弁 OPEN(1.5atm)
17. V2 OPEN. 10分間放置
18. パージバルブ CLOSE
19. V7 CLOSE
20. V2 調節(流量 5ml/min)
21. 熱分解炉 ON(約700度)
22. マイクロ波発生装置 ON. 5分間 N2 放電
23. マイクロ波発生装置 OFF
24. V2 FULL OPEN
25. (フロートが落ちたら)V2 CLOSE
26. V1 CLOSE
27. SiH4 減圧弁 CLOSE
28. SiH4 元栓 OPEN
29. V6 OPEN. 排突筒 N2 置換(300ml/min で5分間)
30. 熱分解炉温度確認
31. SiH4 減圧弁 OPEN
32. V1 OPEN
33. V6 調節(100ml/min)
34. V2 OPEN(必要流量まで) 5分間放置
35. マイクロ波発生装置 ON. 必要時間放電
36. (適当な時に)SiH4 元栓 CLOSE
37. マイクロ波発生装置 OFF. ヒーター OFF
38. V2 FULL OPEN
39. (フロートが落ちたら)V6 CLOSE
40. SiH4 減圧弁 CLOSE
41. パージバルブ OPEN
42. V2 CLOSE
43. SiH4 減圧弁 OPEN(1.5atm)
44. V2 OPEN. 15分間パージ
45. 熱分解炉 OFF
46. V3 CLOSE
47. SiH4 減圧弁 CLOSE
48. (0atm 以下になったら)SiH4 減圧弁 OPEN(0atm)
49. (フロートが落ちたら)V2 CLOSE. 基板取り出す
50. SiH4 減圧弁 OPEN(1.5atm)
51. V1 CLOSE
52. SiH4 減圧弁 CLOSE
53. パージバルブ CLOSE. 続けて運転する場合は7へ
54. N2 減圧弁 CLOSE
55. N2 元栓 CLOSE
56. liq. N2 トラップ はずす
57. トラップ管内排気
58. 排気系 CLOSE
59. ロータリーポンプ OFF. リーク
60. ドラフト OFF
61. 確認
注意事項
SiH4 は空気と混合すると酸素と反応して自然発火するので、空気には触れさせてはならない5)。そのため、基板の出し入れなどで系内に空気が入る場合は、その前後で N2 による置換を、上に示したように十分に行なうことが必要である。また、装置を長時間使用しない場合は、ガラス製の真空系は真空にし、ステンレス鋼製の系は1.5atmの N2で満たしておく。
SiH4 を急速に熱分解するには 600℃以上の温度が必要であるので、熱分解炉は常に 700℃前後に保つ。熱分解炉中の石英管に詰めてあるステンレス鋼片が酸化すると、装置運転中に H2 による還元が起こり、水を生成してしまうので、熱分解炉が 200℃以上の時には、基板の取り換え等で空気を入れるようなことがないようにしなければならない。
参考文献
1)早川保昌, 松本 修, "プラズマ化学とその応用", 裳華房 (1971)
2)阿部英太郎, "マイクロ波技術", 東京大学出版会 (1979)
3)八田吉典, "気体放電", 近代科学社 (1960)
4)C.Mailhiot, J.F.Currie, S,Sapieha, M.R.Wertheimer, A.Yelon, J. Non-Cryst. Solids, 35-36, 207 (1980)
5) 原田 光, 建築設備と配管工事, 10, 55 (1982)
目 次
雑科学ホーム
hr-inoueホーム