雑科学ホーム
hr-inoueホーム
● 微細加工の話 ●
小さいことの価値
最近、新聞などで「ナノテク」という言葉を目にしない日はほとんどありません。現実にはナノメーター(nm = 10-9m)までは行かないマイクロメーター(μm = 10-6m)レベルのものもありますが、とにかく小さい物を扱う技術は花盛りです。かつて「大きいことはいいことだ」というフレーズが流行ったことがありましたが、小さいことの利点もいろいろあります。部品が小さくなれば、それを使った機械装置も小さく、持ち運びに便利になりますし、逆に全体の大きさが同じならば、小さいほど多くの部品が詰め込めて高機能になります。典型的なのがLSIやそれを活用したコンピューターですね。細い配管の中や、場合によっては人間の体の中で活動するロボットなども、「小ささ」の「大きな価値」の一つでしょう。また、単に物理的な大きさの問題だけでなく、小さくすることによって新しい機能が発生することもあります。先のLSIの例では、小さくすることで配線が短くなって動作速度が上がる、ということもあるのです。
微細なものを扱う技術の中には、元々自然界に存在する微小粒子や構造体を利用するものもあれば、人工的に微小なものを作り出す技術もあります。微小物を人工的に作るには、大きな物を粉砕する方法や、化学的に巨大分子(分子で言えば巨大ですが通常のスケールで言えば微小です)を合成する方法などもありますが、ここでは特に、何らかの加工によって微細構造を作り出す技術に注目してみました。
機械的に削る技術
加工の原点は、やはり機械的に切ったり削ったりすることでしょう。彫刻刀で削る、あるいはもうちょっと機械化して旋盤で削る、というような方法を、単純に小さく小さくして行くのです。
電子顕微鏡の話の試料作りに登場するミクロトームなどは典型的な微細機械加工の装置です。残念ながら微細加工できるのは一方向のみですが、その方向に関しては10nmの制御が可能なものもあります。さらに小さな(あるいは2方向3方向の加工が可能な)装置としては、顕微鏡下、あるいは電子顕微鏡下で使うものが実際にあります。これらの装置では、刃先のサイズが小さいだけではなく、その動きをどうやって精密に制御するかが重要で、さすがに機械的なカラクリだけでは限界があるので、電圧をかけると伸び縮みする圧電素子(ピエゾ素子)が使われる場合もあります。
同じように「機械的に削る」と言っても、金属やセラミックスの刃物で削るのではなくて、レーザーやイオンビームを使う方法があります。イオンビームを使う装置として収束イオンビーム(
Focused
Ion
Beam = FIB)加工装置がありますが、これについては
電子顕微鏡の話で説明していますので、ここでは省略します。
レーザーを使う加工装置としては、パワーのある炭酸ガスレーザーを使ったものが有名です。炭酸ガスレーザーは
気体レーザーの一種で、単位面積当たりに換算すると、地表での太陽光の数百万倍ものエネルギーを作り出すことができます。この強烈なエネルギーを使って、金属をはじめ様々なものを切断できるのです。また炭酸ガスレーザーの光は水に吸収されやすいので、水分の多い生物の組織を切断するのに有効で、手術の道具としてメスの変わりに利用されたりもしています(もちろん、金属などを切る場合と比べて出力は大幅に落としてありますが)。ただし炭酸ガスレーザーの光は波長が10μm程度の赤外線ですから、このレベルよりも小さく絞ることはできず、ビームの直径は通常は0.1mmぐらいです。そのため、0.1mm以下の微細加工には向いていません。
エレクトロニクスを支えるリソグラフィー
微細加工技術の中で我々が最も恩恵を受けているものの一つが、半導体の加工などに用いられているリソグラフィー(Lithography)でしょう。Lithoとは石のことですから、元々Lithographyとは石版のことを意味しています(よく美術の本などにリトグラフという石版画が出ていますが、これのことです)が、この言葉が半導体などに微細な回路を刻む技術に対しても使われているのです。シリコンという「石」にミクロな彫刻を施す、という感じでしょうか。もちろん彫刻刀で刻むわけではなくて、普通は光を使って感光性の材料にパターンを焼き付けることを基本にしていますので、フォトリソグラフィー(Photolithography)と呼ばれています。
フォトリソグラフィーの技術は、
ハードディスクの話でも紹介している磁気ヘッドや、微細な歯車などを作るマイクロマシンなどの分野でも使われています。しかし、やはり何と言っても有名なのは半導体素子でしょう。以下に、主に半導体加工の例を引きながら、フォトリソグラフィーの概要を見てみることにします。
リソグラフィーの鍵を握る材料 ― フォトレジスト ―
フォトリソグラフィーの基本は、フォトレジスト(あるいは単に「レジスト」)と呼ばれる感光性の材料に光を当ててパターンを焼き付けることにあります。その概略を図1に示しました。フォトレジストとは、要するに光が当たると何らかの反応を起こして、溶媒に対する溶けやすさが変化する材料のことです。

図1 フォトリソグラフィーの基本はフォトレジストのパターン形成
シリコンなどの半導体基板にフォトレジストの溶液を塗布し、望みの形に窓を開けたフォトマスクと呼ばれる覆いをかけて光に当てます(露光)。すると窓の部分のフォトレジストだけが光に当たり、溶媒に溶けやすくなったり、逆に溶けにくくなったりしますから、後で適当な溶媒で洗ってやれば、フォトマスクのパターン通りにフォトレジストを残すことができるのです(現像)。この時、光に当たった部分が溶けにくくなるタイプをネガ型レジスト、溶けやすくなるタイプをポジ型レジストと呼んでいます。なぜこう呼ばれるかは、フォトマスクのパターンと、残ったレジストのパターンを比べてみればわかります。フォトマスクの孔の部分(つまり光が通る明るい部分)がそのままレジストの孔になって「明」−「明」という対応になっているのが「ポジ」、逆にフォトマスクの孔の部分が塞がって「明」−「暗」の対応になっているのが「ネガ」です。銀塩写真でも、光の当たっていない部分の銀が洗い流され、光の当たったところだけ銀が残って黒くなったフィルムをネガと呼びますから、同じことですね。
露光の時に被せるフォトマスクとしては、本当に孔の開いた板を使う必要はありません。透明なガラスに部分的にクロムなどの金属を付着させたものが一般的です。また、図1ではフォトマスクを直接に基板に乗せて露光していますが、実際にはフォトマスクは大きめに作っておいて、映写機の原理(
光学機器の話参照)でその縮小像をレジスト上に投影して露光する方法がよく使われます。基板の方を順送りにしながら次々に露光して行きますので、このような露光装置のことを「ステッパー」と呼んでいます。
ネガ型レジストには、主に光を当てることで重合して高分子になるような物質が使われます。いわゆる「光硬化性樹脂」の類です(図2(a))。光に当たらなかった部分は現像の時に溶け出すのですが、水系の溶媒には溶けない場合が多いので、現像には有機溶媒を使うことが多くなります。ところが、樹脂類は有機溶媒に溶けないまでも多少は溶媒を吸収して膨らむ傾向がありますから、寸法精度が悪くなる、あるいは吸収された溶媒が後の工程でなかなか取り除けない、といった問題が起こることがあります。また、空気中の酸素が邪魔をしてうまく硬化できなかったり、反対に容器に入れて保存している間に勝手に硬化反応が進んでしまったり、という扱いにくさもあって、半導体のリソグラフィーでは主役の座をポジ型に譲ることが多くなっています。
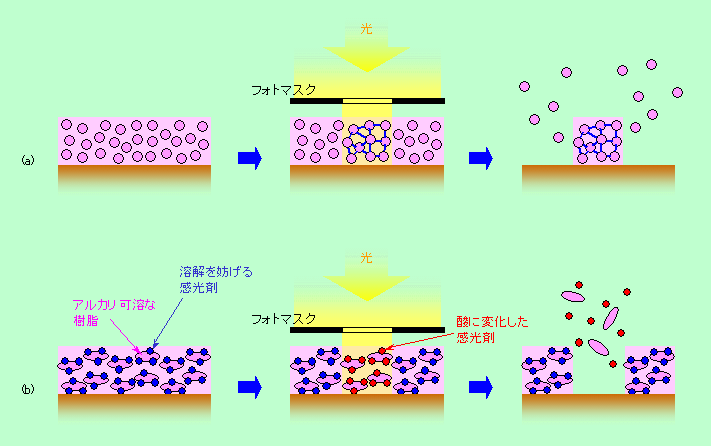
図2 フォトレジストが感光する仕組み
(a) ネガ型 (b) ポジ型
ポジ型レジストは一般に感光剤と樹脂の混合物です。樹脂自体はアルカリ水溶液に溶けるタイプのものですが、樹脂分子の中の溶解性にかかわる部分を感光剤分子が押さえ込んでいて溶解しなくなっています。これに光が当たると感光剤が変化を起こして酸に変わりますので、図2(b)のように感光剤自身も、タガが外れた樹脂も、アルカリに溶けるようになるのです。また最近では、アルカリに溶けやすい部分を別の化学構造に変えて溶解しにくくした樹脂を使ったポジ型レジストもあります。この場合は光によって感光剤から発生した酸が、その急所(化学構造を変えた部分)を攻撃して、元のアルカリに溶ける形に戻すのです。しかも、元に戻る時にまた新しく酸を発生させますので、それが別の急所を攻撃して・・・・ということを繰り返し、どんどん反応が進みます。光が少なくても効率よく反応が進む、つまり高感度のレジストという意味で、このタイプを「化学増幅型レジスト」と呼んでいます。普通は高感度にすると保存中にも反応が進んでダメになってしまうおそれがあるのですが、化学増幅型レジストの場合は、感光剤自体の感度が上がっているわけではないので、使用直前に樹脂と感光剤を混ぜるようにすれば、保存上の問題は発生しません。
露光用の光にもいろいろ
露光には可視光線や紫外線が使われますが、光には陰の部分に回り込む「回折」という現象があって(
立体映像の話参照)波長程度のボケが必ず存在しますから、細かいパターンを作ろうとすれば、それに応じて波長の短い光を使う必要があります。そのため半導体素子の製造では、より微細な加工が必要になるにつれて、時代と共に可視光線から紫外線、紫外線の中でもより波長の短い光へと主役が移って来ています(もちろん、それに合わせてフォトレジストの方も改良されて来ています)。光学の世界でg線だとかi線などという呼び方をよく使いますが、これらを含めて、よく使われる露光用の光を表にまとめてみました。
表 露光用の光
|
呼称 |
波長(nm) |
光源 |
可視光線 |
g 線 |
436 |
高圧水銀ランプ |
h 線 |
405 |
高圧水銀ランプ |
紫外線 |
i 線 |
365 |
高圧水銀ランプ |
|
254 |
低圧水銀ランプ |
|
248 |
KrFエキシマレーザー |
|
193 |
ArFエキシマレーザー |
|
157 |
F2エキシマレーザー |
|
13.5 |
EUV光源 |
g線は1960年代後半、まだ集積回路がIC(Integrated Circuit)と呼ばれていた時代から使われていました。このころのパターンの最小幅(線幅)は10μmぐらいで、まだまだ黎明期です。g線の時代は1970年代〜1980年代も続き、その間に線幅は1μmを切るところまで小さくなりました。線幅が半分になると面積は4分の1にできますから、全体の容量はざっと4倍になります(実際には素子の構造の工夫などで、線幅が半分まで行かなくても4倍容量のものが作られています)。代表的な半導体素子であるDRAM(Dynamic Random Access Memory)の容量で言えば、1970年代初めの1kbit(線幅8μm)から4kbit(6μm)、16kbit(4μm)、64kbit(2.5μm)、256kbit(1.5μm)と進んで1980年代後半には1Mbit(1.2μm)、4Mbit(0.8μm)まで来ていました。
1980年代末から1990年代にかけてはi線の時代です。線幅は1μmを大きく割り込んで、16MbitのDRAMで線幅0.5μmまで来ましたが、i線の波長は365nm(0.365μm)ですから、このあたりから、「光による露光はもう限界で、これからは電子線かX線」と言われるようになりました。ところが、切羽詰って来るとまたいろいろなアイデアが出るもので、例えば図3のような光の干渉を利用した技術が登場して来ます。
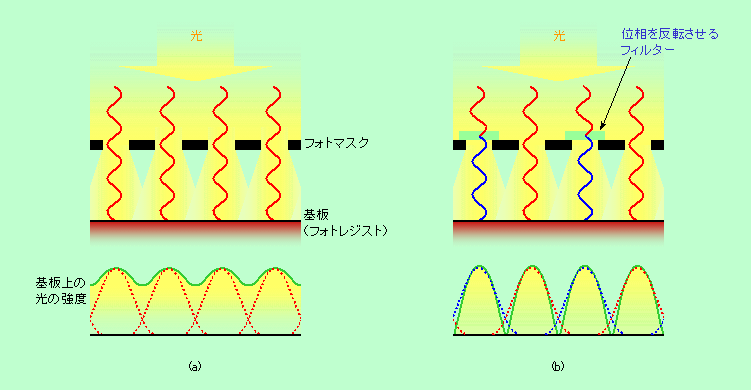
図3 波長の限界を超える方法
図3(a)のように狭い間隔で隙間の空いたフォトマスクを通して光を当てることを考えます(レンズによって像を作る部分は省略)。通常ならば、マスクの形そのままに明暗のパターンが基板上に投影されるはずです。ところが光には波長程度の大きさのボケがありますので、明暗の間隔が光の波長と同じぐらいまで狭くなって来ると、ボワッと広がった光が隣どうしで重なるようになります。その結果、下側の光の強度の図が示すように、マスクの孔を通って来た光(赤の破線)が重なり合って、緑線のような明暗がはっきりしないパターンになってしまうのです。そこで、マスクの孔に一つおきに光の位相を180度ずらせる(つまり波の山と谷の位置を逆転させる)フィルターをかける、という方法が考えられました(図3(b))。このようにすると、位相がずれた光どうしは互いに打ち消し合いますから、隣どうしで重なった部分の光が弱められ、フォトマスクと同じピッチの明暗が再びはっきりと現れるのです。この図では最終的に光が当たる部分の幅がマスクの孔よりも広くなっていますが、マスクの方であらかじめパターンの幅を調整しておけば、望みの明暗パターンを得ることができます。これが光の波長の限界を突破する方法のひとつ、「位相シフト法」です。これらの方法を駆使して、波長よりも小さい線幅0.35μm、DRAMの容量で64Mbitまでi線で到達してしまいました。
しぶとく生き延びたi線ですが、さすがにここから先は厳しく、またもや「光は終わり」という声が聞こえ始めます。ところが再び救世主が現れます。新しい光、エキシマレーザー(
発光の話参照)の登場です。まず初めに実用化されたのは波長248nmのKrFレーザーで、1990年代半ばには線幅0.25μm、DRAM容量256Mbitが達成されます。さらに1990年代後半には波長193nmのArFレーザーが出て来て、ついに1Gbitを超えるDRAM容量に突入するのです。エキシマレーザーとしては、もう一ランク上のF
2レーザーも使われ始めています。
このさらに先、ということになると、紫外線と言ってもむしろX線に近い領域に入って来ます。表にあるEUV(
Extreme
Ultla
violet)がそれで、プラズマの発光を利用した特殊な光源を使います。エネルギーが高すぎて材料自体を破壊してしまうためにレンズが使えず、反射を使った精密な光学系が必要だとか、フォトマスクにも耐久性が要求されるとか、課題はたくさんありますが、これからどのように展開して行くのか注目されるところです。さらに波長が短くなってX線の領域に入ると(どこが紫外線とX線の境目なのかは、はっきりしませんけど)、シンクロトロン放射光(
Synchrotron
Orbital
Radiation = SOR)と呼ばれる光が有力になって来ます。光の速度に近い超高速で走る電子が磁場で曲げられた時に放つ光を利用するもので、普通は電磁石で加速した電子をドーナツ型の真空容器の中でぐるぐる走らせる方式です。SOR光はX線から赤外線までの幅広い波長を含んだ強烈な光で、いろいろな用途に使われていますが、特に強度が高いのがX線の領域で、これをリソグラフィーに利用しようというわけです。ただし、SOR光に限らずX線をリソグラフィーに使おうとすれば、これをうまく遮断してくれるフォトマスクに苦労することになります。何せ物質を透過する能力の高いX線ですから、かなり重い金属で精密なパターンを作る必要があるのです。また、SORは設備が大きくなるのも難点の一つです。素粒子の研究に使われている直径何キロ、というような施設は別にしても、小型のSOR装置でも直径は1mぐらいあり、その周りの付帯設備を含めれば、結構大きな部屋を占拠してしまいます。
もうひとつ、普通の電磁波とは毛色の違うものとして、電子線があります。電子線は、波長という意味では電磁波と比べ物にならないほど短い(
電子顕微鏡の話で書いているように、100kVで加速された電子線の波長はわずか0.0000037μm)ですから、波長から来る限界はまず問題になりません。電子がフォトレジスト中で散乱することから来るボケはありますが、光と比べるとはるかに細かい、0.01μmレベルのパターン形成が可能です。この電子線による方式には、光の場合と同じように電子線を広い面積に降らせてフォトマスクを通して露光する方法と、フォトマスクを使わないで、細く絞った電子ビームで線画を描くようにパターンを露光して行く方法とがあります。フォトマスクを使う方法は光を使った方法の延長で手軽ですが、さすがに光ほど大面積を一度に露光することはできませんので、効率は悪くなります。電子線を使ったリソグラフィーが大量生産になかなか使われない大きな理由の一つが、この効率の悪さです。効率という面では、電子ビームで描画するもう一つの方法はさらに悪くなります。しかし複雑な細工が思い通りにできますから、臨機応変の柔軟性は抜群で、私の知人はこの方法で半導体のウエハに精密な地図を描いたりもしていました。
このように精密なパターン形成は得意でも大量生産には向かない電子線リソグラフィーですが、実は既に半導体産業で活躍している領域があります。これまで再三出て来たフォトマスク。これを作るのに使われているのです。時間はかかるものの精密な細工ができる方法で、とりあえず精巧なマスクを作っておき、後はこのマスクを使って光リソグラフィーで同じパターンを大量生産するのです。
材料のエッチング
図1の工程ではフォトレジストのパターンができただけですから、次にこれを利用して下地の材料そのものを加工する必要があります。フォトレジストで保護されていない剥き出しの部分を削ったり溶かし出したりする、エッチングと呼ばれる操作です。エッチングというのは、元々は金属などを腐食性の液に浸して、表面を保護していない部分を腐食加工する技術のことですが、これを材料を削り取る技術全体に広げているのです。ついでに言うと、「レジスト」という言葉の元の意味は「防食材(腐食防止材)」です。まさに「エッチングから基材を保護する防食材」なのです。
エッチングの方法には大きく分けて2種類あります。本来のエッチングの意味に近い、薬液に浸して溶かす「ウェットエッチング」と、液を使わない「ドライエッチング」です。ウェットエッチングは、一度にたくさんの基板を処理でき、材料に余分なダメージを与えることも少ない簡便な方法です。薬液としては、シリコン酸化膜にはフッ化水素酸、シリコンには硝酸などの酸化剤とフッ化水素酸の組み合わせ、ガリウム-ヒ素(Ga-As)やインジウム-リン(In-P)などの化合物系の半導体や金属には硫酸、塩酸、硝酸などの酸がよく使われます。実際には単独成分でエッチングすることは稀で、エッチングの速度や半導体結晶に対する方向性(結晶の特定の方向が溶けやすい、ということはよくあります)、基板へのダメージ等を考慮して、複数の成分を組み合わせた複雑な組成の薬液が使われています。
ウェットエッチングは設備も安価でいいのですが、図4(a)のように横方向にもエッチングが進むという欠点があります。この影響は深くエッチングするほど大きく、パターンの幅が不正確になります。せっかくフォトレジストで正確なパターンを作っても、エッチングの工程で台無しになってしまうのです。そのため最近では、精度の高い加工ができるドライエッチングが大きな割合を占めるようになっています。ドライエッチングでは一度に処理できる基板の数が限られますし、設備も割高なのですが、どんどん小さくなって行く加工寸法に対応するには、ウェットエッチングだけでは無理があるのです。
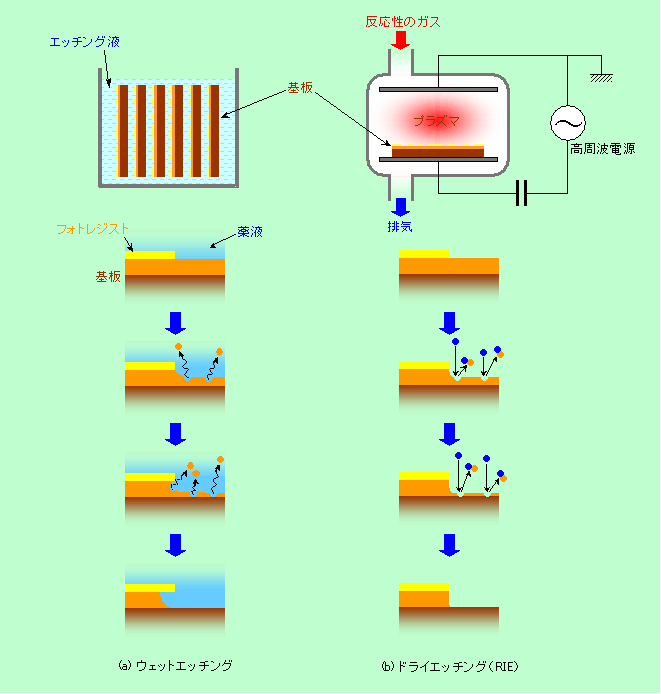
図4 ウェットエッチングとドライエッチング
ドライエッチングでは、真空容器中で、低圧のガスに電圧をかけて作り出したイオンを基板にぶつけます。ここで、単純に勢いだけで基板の物質を物理的に叩き出すのが最も簡単なのですが、叩き出した物質を別の基板上に積もらせるいわゆるスパッタリングとは目的が違いますから、もっと精度の高い別のプロセスが主流です。これが図4(b)に示した反応性イオンエッチング(Reactive Ion Etching = RIE)です。この方法では、イオンがぶつかることによる単純なスパッタリングの効果もありますが、ガスが分解して発生する反応性の高い物質が基板の材料と反応して揮発性の化合物を作り、外に排気される、という化学的な作用がポイントになります。そのため、単純なスパッタリングでは極端に言えばガスの種類は何でもいいのですが、RIEではエッチングする相手の材料と反応して揮発性の高い化合物に変化する物質を使う必要があります。例えば、相手がシリコンならば6フッ化イオウなど、シリコン酸化物ならば4フッ化炭素など、銅ならば塩素など、というぐあいです。この方法ならば相手の原子を1個1個反応させて剥がして行くことができ、ぶつける方向をコントロールしてやれば横方向へのエッチングも防げますから、精度の高い加工が可能になるのです。
RIEの作用のうち化学反応の方は相手を選びますが、物理的なスパッタリングの方は基本的に相手が何であっても進行しますから、保護する役目のフォトレジストもドライエッチングの過程で相当に削られます。それでも皮一枚残っていれば下地を保護する役目は果たせますから、初めに十分な膜厚にしておけば問題はありません。
エッチングが終われば、あとは不要になったフォトレジストを取り除くだけです。ポジ型レジストの場合は、残っている未露光部を改めて光に当てれば溶けるようになりますが、ネガ型レジストの場合は変質してエッチング用の薬液には溶けなくなっていますから、溶かすには別の薬液を準備する必要があります。ただし、ポジ型であっても、(ウェットでもドライでも)エッチングの過程でフォトレジストが変質することはあります。元々は無かった化学結合ができて高分子化する場合もあり、フォトレジストを溶かして除去する時にはそれなりの薬剤を選択する必要があります。あるいは、酸素のプラズマなどで燃やしてしまうドライな方法(酸素プラズマエッチング)もあります。これだと大抵の有機物は除去できますが、下地もやられてしまうことがあるので、フォトレジスト表面の変質層だけプラズマエッチングで除き、あとは薬液で溶かす、というやり方も多くなっています。
乗っけて剥がす、リフトオフ法
フォトレジストのパターンを使って加工する方法としては、「不用部分を取り除く」エッチングの他に、「必要なものを付着させる」方法も使われます。原理は単純で、フォトレジストパターンの上から蒸着などの適当な方法で膜を付け、フォトレジストもろとも剥がしてしまうのです。これが「リフトオフ法」で、金属の配線を付けたりする時に用いられます。金属の接合に使われるハンダが剥離を起こす現象も「リフトオフ」と呼ばれていますが、このような好ましくない話とは違って、リソグラフィーの世界で立派に役立つ技術です。
リフトオフ法の概要を図5に示しました。フォトレジストにネガ型とポジ型があることは既に説明しましたが、一般にリフトオフにはネガ型の方が適しています。その比較も図に併せて載せておきました。
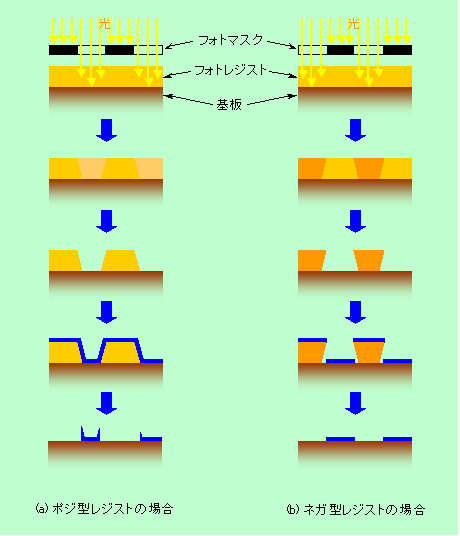
図5 ポジ型とネガ型のフォトレジストを使ったリフトオフ法
フォトレジストを露光する時、表面から奥まで同じ強さで光が当たるわけではありません。光を受けて何らかの変化を起こすということは、光のエネルギーを吸収するということですから、当然、奥に進むほど光は弱くなります。ポジ型レジストの場合、光が当たった部分が溶けるわけですから、奥に行くほど溶けにくくなり、下に向かって広がった台形のレジストが残ることになります。これを使ってリフトオフを行なうと、望みのところでスパッと切れたパターンになりにくいのです(図5(a))。これに対してネガ型の場合は、奥に行くほど固まり方が悪くなりますので、上部がせり出した崖のような形にレジストが残ります。これに上から金属を蒸着すると、崖の真下には付着しませんから、不要な部分の金属だけがきれいに除かれるのです(図5(b))。もちろんポジ型レジストでも、縁の部分をあらかじめ切り落とす操作を加えたり、金属膜の付着のさせ方を工夫したりすることで、きれいなリフトオフが実現できますが、手軽な操作だけでうまくやろうとすれば、ネガ型レジストの方が有利なのです。
このような技法を駆使して、よくエレクトロニクス関係の雑誌などで目にするあの複雑な構造の素子が作られます。図6に、素子が組み上げられて行く例を大雑把に示してみました(フォトレジストを塗ったり取り除いたりする工程は省略しています)。フォトレジストを使ってパターンを切り、上から次の材料(導電材、絶縁材など)を付け、それをまた削り、という工程を何十回も繰り返して、何階建てもの積層構造を作り上げて行くのです。
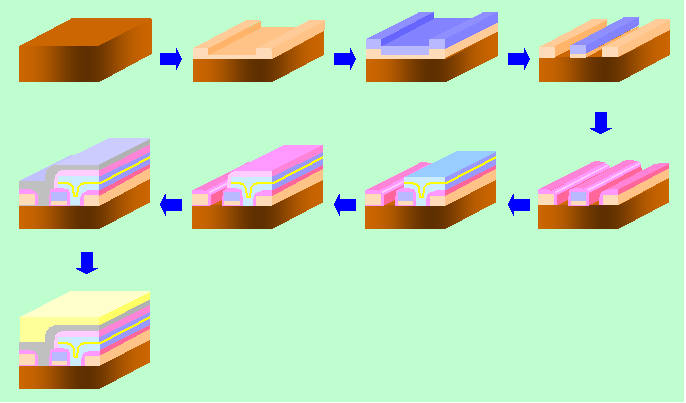
図6 半導体素子が組み上げられて行く工程
図に示した部分自体はμmレベルの微小なもので、このような構造(セルと呼びます)が何千万個もぎっしり敷き詰められて1個のLSIが構成されます。1枚のシリコン基板(円板状のウエハ)の上にはたくさんのLSIの回路が同時に作られますから、1枚の基板にはそれこそ億単位のセルが乗っているのです。
マイクロマシンへのリソグラフィーの応用
リソグラフィーの技術が半導体以外にも使われていることは既に書きましたが、中でもマイクロマシンの分野は最近注目されています。モーターだとかポンプなどと言った、電気エネルギーを与えて何らかの機械的な動作をする仕組みですので、「Micro Electro Mechanical Systems(MEMS)」とも呼ばれます。普通の電気機械のように部品を別々に作って組み立てるやり方では限界がありますから、リソグラフィーを使って、いろいろな部品が組み上がった形を削り出して行くのです。
マイクロマシンが先ほどの半導体素子と大きく違っているのは、機械的に動く部分があるということです。そのためには必ず、周囲から切り離されて宙に浮いたような、あるいはごく一部だけで支えられて空中に突き出たような構造が必要になります。つまり、上から溝を掘るだけでなく、部品の下側(裏側)も削らなければならないのです。リソグラフィーでこのような加工をするためには、まず土台となる層を形成してその上に必要な部品を作り、後で土台層を取り除く、という方法が採られます。この後で取り除かれる土台のことを「犠牲層」と言います。図7に、このような犠牲層を使ったMEMSのプロセスをごく簡単に示しておきました(実際のMEMSプロセスの複雑さはこんなものではありませんが)。
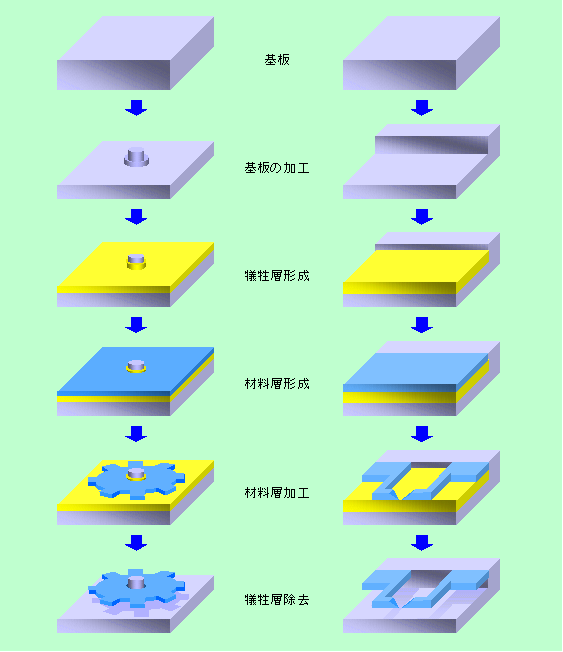
図7 犠牲層を使ったマイクロマシン(MEMS)プロセスの簡単な例
犠牲層を取り除くのにも、半導体の加工と同じエッチングの技術が使われます。液体で溶かし出すウェットな技法と、プラズマなどで分解して飛ばすドライな技法が使い分けられている点も同様です。ただし、普通のRIEなどは上からの加工しかできませんから、向きを変えていろいろな方向から削ったり、反応性のガスが裏側まで回り込むように装置を工夫したりすることは必要です。また必要な部分まで削ってしまっては困りますから、犠牲層に使う材料の種類やエッチングの方法は慎重に選ばなければなりません。
光で目的物を直接加工する方法
半導体のリソグラフィーでは光で加工するのはフォトレジストだけであり、目的の材料はレジストのパターンをマスクにしてエッチングで削っていました。しかし、十分な強度が得られるのであれば、感光性の材料自体で最終的な目的物を作ることもできます。要するにフォトリソグラフィーの技術を使った直接加工ということで、ネガ型レジストと同類のアクリル系樹脂の成型などがその代表例です。適当なフォトマスクを通して露光してやれば、マスクの孔の形通りに固まった樹脂成型体ができるので、実際にプラスティック製の部品の製造に使われています。また、レーザービームを走査して文字や絵を描き、印刷用の原版を作る、という利用方法もあります。出来上がった版は、光を当てた文字の部分が飛び出た凸版になります。いわゆるフレキソ印刷ですね。
光による直接成型で面白いのは、平面的ではなく3次元の立体成型ができることです。図8のように、レンズの焦点距離を変えて望みの深さに光が集まるようにしたり、複数の方向からビームを入れて重なった部分だけが硬化するようにしたりして、一気に3次元の彫刻を仕上げてしまうのです。物体の形を立体的に計測し、そのデータを基に光硬化性樹脂を使って全く同じ形をその場で作り出す、3次元コピー機のようなものも実際に作られています。
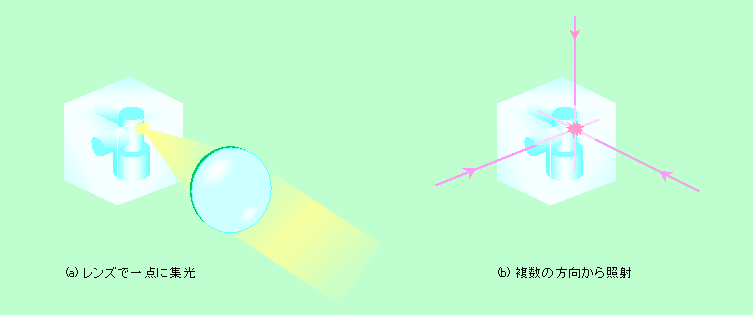
図8 光を使った3次元成型
リソグラフィーとメッキと鋳型成型の融合 ― LIGA ―
普通のリソグラフィーは、微細なパターンも幅広のパターンも横方向ならば自在にできますが、縦方向(深さ方向)はあまり大きくできません。フォトレジストをマスクにして掘り進む場合、あまり深くなると、たとえドライエッチングであってもレジストの形状からズレてしまいます。同じことは光で直接材料加工する場合にも言えて、奥に行くほど光が広がって精密な細工ができなくなるのです。その一方でマイクロマシンなどでは、非常に深く切り込まれた形状が要求される場合が多々あります。幅1μmで深さが100μm、などという形が必要なこともあるわけで、このような要求に応える技術の一つとして注目されているのが、ここで取り上げるLIGAです。
LIGAというのは元々ドイツで開発された技法で、リソグラフィーとメッキと鋳物の技術を組み合わせたものです。それぞれのドイツ語表記、「Lithographie(リソグラフィー)」、「Galvanoformung(電気メッキ、電鋳)」、「Abformung(鋳型成型)」からLIGA(リガ)と呼ばれています。そのプロセスの概要を図9に示しました。
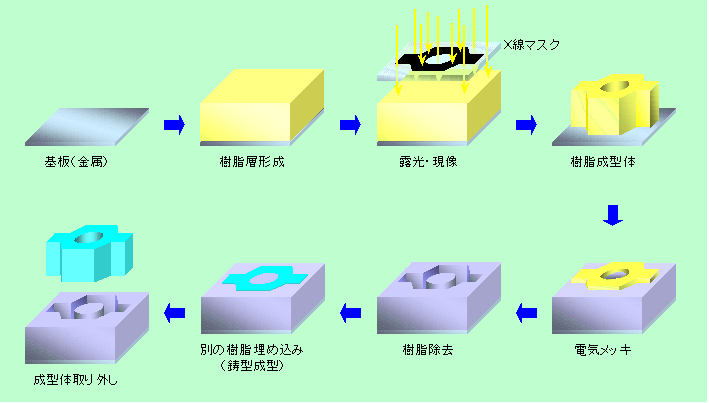
図9 LIGAのプロセス
リソグラフィーの部分では、半導体の加工などと比べてずっと深いところまで精密に細工しなければなりませんから、一般的な光は使えません。奥深くまで弱まらずにまっすぐに届く強烈な光が必要で、先にX線リソグラフィーのところでちょっと出て来たシンクロトロン放射(SOR)のX線が使われます。X線の場合、紫外線のように光硬化性の樹脂を固めるというよりも、既に固まっている樹脂をズタズタに壊して取り除く方が得意ですから、図のようなポジ型のパターンを使うのが普通です。金属板の上にアクリル樹脂(メタクリル樹脂)を塗って固め、SORのX線を当てると、マスクをかけた以外の部分が壊れてなくなるのです。この時の下地の金属板がミソで、これが次の電気メッキの工程で電極として働きます。
次の段階は電気メッキです。リソグラフィーで作った型をメッキ液に浸し、下地の金属と対極の間に電圧をかけて、樹脂を除去した部分にニッケルなどの金属を積もらせるのです。図ではものすごく厚く描いていますが、実際のメッキ厚さは普通1mm以下です(それでも通常のリソグラフィーと比べればはるかに厚いですが)。
メッキを終えた後に残った樹脂を取り除けば、金属の型が残ります。この型をそのまま金属部品として使うこともできますが、これを鋳型にして別の樹脂の成型体をどんどん作って行けば大量生産ができます。LIGAの大きな特徴の一つは、この大量生産性にあると言ってもよいでしょう。前にも書いたように、SORは非常に大掛かりで高価な設備ですから、これを使って一個ずつしか部品が作れないとなると、とんでもなく高くついてしまいます。しかし大量生産ができるとなれば、使いようによっては採算が合うようにもなり得るのです。とは言うものの、やはり簡単にできる加工法ではありませんから、X線ではなくて紫外線を使ったLIGA風プロセスもいろいろと検討されているようです。
原子を1個ずづ操作する ― 究極の微細加工 ―
加工のサイズをどんどん小さくして行くと最後はどうなるでしょうか。その行き着く先は「原子1個」です。原子を1個1個操作して望みの形に組み上げる・・・これぞ究極の微細加工です。そんなSFの世界のようなことが実際にできるのか、と思われるかもしれませんが、実用レベルではないものの、既にたくさんの例があります。
1981年の走査トンネル顕微鏡(STM)の発明がそのきっかけでした。電圧をかけると伸び縮みするピエゾ素子を利用して微小な針を試料の表面で動かし、その時に針と試料の間で流れる電流を感知して試料の表面形状を原子レベルで測定する装置です。針と試料が接触すると試料にダメージを与えてしまいますから、ギリギリ接触しない距離に針を置いて、空間を隔てて流れるトンネル電流を測るのがポイントです。これを逆手に取ると、試料に直接針を接触させたり、試料の原子のすぐそばで針に電圧をかけたりすれば、原子レベルで試料を操作することができるはず・・・・。というわけで、1990年に原子で書いた世界最小の文字の映像(STMの観察像)がアメリカで公表されました。極低温(-269℃)に冷やした状態でニッケル板の上吸着した35個のキセノン原子を並べ直すことで文字を描き出したのです(温度が高いとニッケルに吸着したキセノン原子が勝手にフラフラ動いてしまうので極低温に冷やしています)。一般の新聞にも掲載されましたから、見た人も多いでしょう。ついにここまで来たか、という感じで、これはなかなかインパクトがありました。
翌年には日本でも、さらに小さい文字が発表されました。前年のものが飛び出た文字、つまり「陽刻」であったのに対し、今度の文字は硫化モリブデンの表面からイオウ原子を弾き飛ばした跡にできる窪みで描いた「陰刻」でした。その後もいろいろな文字や絵が様々な手法で描かれています。
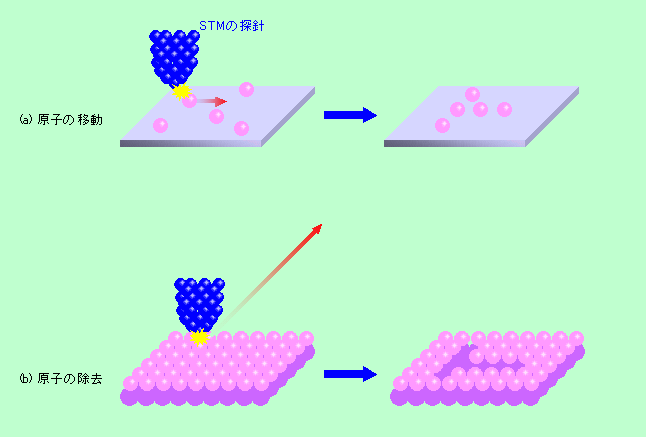
図10 原子で文字を描く
このように夢のある技術ですが、何しろ時間と労力がかかりますから、今のところは工業製品を作るという段階ではありません。原子操作単独で何かを作る、という域に達するには、まだまだ時間がかかりそうです。しかし、他の方法と組み合わせてなら、可能性はあります。例えばリソグラフィーなどで作った構造に最後の微調整を施す、とか、原子操作でしか作れない微細な構造を素子の一部に作り込む、といった使い方です。あるいは化学的な方法との組み合わせで、分子や結晶を作るように原子が自分で並ぼうとする性質を利用して加工することも検討されています。また、1個の針で細工するのに時間がかかり過ぎると言うのなら、多数の針をびっしり並べていっぺんに加工してしまえばよい、という発想で、先のMEMSの手法でそのような加工装置を作る試みもあります。いずれは、原子操作で作った製品が家庭に入り込んで来る日が来ることでしょう。
雑科学ホーム
hr-inoueホーム